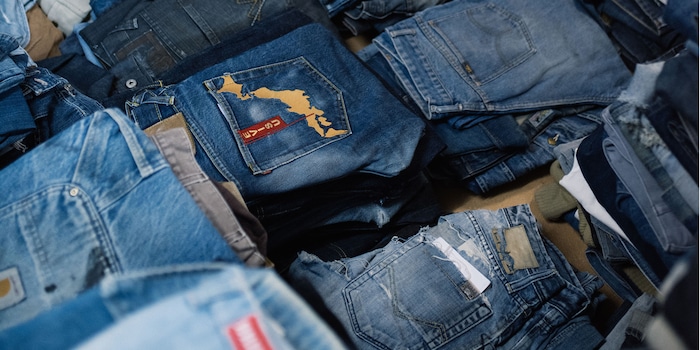
Sustainable denim of tomorrow

Fashion group Fast Retailing has big plans for its "Denim Innovation Centre". The Japanese fashion group wants to produce its denim trousers sustainably.
In order to drive forward the development of new jeans technologies and trends, the fashion group Fast Retailing opened the "Denim Innovation Centre" in Los Angeles three years ago. The innovation centre enables the Japanese company to manage the entire development process of its jeans production internally and accelerate the individual work steps. The focus is on environmentally friendly processing and production methods.
Black sheep
The fashion industry is the second biggest polluter after the oil industry. The denim industry is in pole position both ethically and ecologically, as vast amounts of water and chemicals are needed to produce a single pair of trousers. According to Greenpeace, this amounts to around 1.7 million tonnes of chemicals for two billion pairs of jeans. As more and more people are becoming interested in sustainable fashion, the industry is rethinking its approach. That's why alternative production processes need to be found quickly.
Four wins
For its green mission, the "Denim Innovation Center" is relying on a four-point plan to reduce the waste of water - according to Greenpeace, 7,000 litres of water per pair of jeans - time and manual labour. Technologies such as a laser engraving system, nano-bubbles, ozone washing and a water recycling system are said to reduce water consumption by up to 90 per cent.
The laser engraving system not only reduces the amount of chemicals required, but also the time spent on the manual work process, which is usually carcinogenic. Because the laser automatically burns the used look into the trousers within seconds, up to 60 pairs of jeans can be processed per hour instead of ten by hand. [[image:27041429 "The cotton fabric for future jeans in the production process."]]
The company relies on nano-bubble technology for the popular "stone-washed effect". This reduces waste. This is caused by the pumice stone previously used in the washing process, which contaminates the water with the stone abrasions. Artificial stones are now being used. In contrast to pumice stone, these polymers hardly need to be replaced. This also reduces water consumption.
In order to remove indigo residues from jeans without water and bleach, ozone washing is used. With this technology, the bleaching process of the trousers is initiated with an oxygen shower. This eliminates the use of toxic chemicals in this step.
In addition, the water recycling system from the "Denim Innovation Center" recycles water that has already been used, which is also intended to further minimise the consumption of fresh water.
Fast Retailing is aware that these four measures in the manufacturing process are just a drop in the ocean. The Japanese textile giant already has other projects up its sleeve to reduce its ecological footprint in the long term. Among other things, it wants to use 100 per cent sustainable cotton for all its clothes by 2025.
Follow me by clicking on the button at my author profile if you want to keep up to date with the latest fashion news.
Opening image: Thomas Kunz

When I’m not exploring the depths of the sea as an open water diver, I enjoy plunging into the world of fashion. On the streets of Paris, Milan and New York is where I keep my eyes peeled for the latest trends. And I’ll show you how to take them from the catwalk to your everyday life.