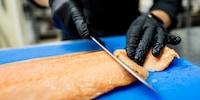
Background information
Chopping boards: wood or plastic, that is the question here
by Martin Rupf
Scientists at universities such as ETH Zurich are working flat out on innovative retort materials that will make the fashion industry more sustainable in the future.
What lasts a long time will (hopefully) finally be good. Climate change is also leading to a rethink in the fashion industry. Slowly but steadily, it is venturing into something new. New things that are possible thanks to technological advances. In addition to more environmentally friendly production methods, the focus is on sustainable materials from the laboratory. They are not only sustainable, but are also intended to be the key to reducing the fashion industry's carbon footprint. In addition to accessories made from sweat, and garments that are coloured with bacteria, fungal cultures and a bio-foam also sound promising.
A pioneer in the field of retort leather is Bolt Threads, based in San Francisco. The start-up laid the foundations for the development of sustainable materials back in 2009. Several years of development and several financial injections later, the biotech company presented "Mylo" for the first time two years ago: A vegan leather that is confusingly similar to tanned animal skin in terms of feel and appearance.
Mylo is based on mycelium, the root structure of fungi. Bolt Threads cultivates cells of this fungal network in the laboratory on organic materials such as sawdust. After around one to two weeks, it joins together to form leather-like material. Because the surface structure can be cultivated as required, the researchers can also use it to recreate crocodile and snake leather.
The start-up has just announced that it is teaming up with various luxury and sports brands: labels such as Adidas and Stella McCartney will launch the first products made from Mylo in 2021. We are talking about several hundred million square metres of vegan leather, which will be processed into sustainable garments and accessories.
The New York biotech company Modern Meadow is also working on a vegan leather alternative. Because collagen is the basis of animal and human connective tissue, the researchers are cultivating a collagen-producing gene from yeast. This is fermented in the same way as in beer brewing. This is used to grow "Zoa", a liquid and customisable organic leather that looks like real leather after cleaning and tanning.
In the meantime, the scientists have discovered that plant proteins also have similar properties to yeast when they are modified. "Customize" is the magic word: depending on the desired elongation, colour and material thickness of the end product, Modern Meadow selects the appropriate building block in advance.
Thanks to this innovation, garments will no longer have to be sewn together in future, but can instead be joined together. This allows designers to customise their patterns before sewing and avoid excess material. The start-up is already in negotiations with various fashion labels. However, it will be a while before the collaborations are ready to be finalised.
The ETH Zurich project is also still in its infancy. The university wants to use a novel process to produce a test-tube foam from organic waste. The difficulty with foam alternatives lies in the fact that a plastic only foams up when a blowing agent is added and exposed to high heat. This is the only way to make foam elastic. As biowaste is sensitive to heat, it is difficult to make the end product elastic. A new type of foaming agent, consisting of water and gas, which foams up even at low temperatures and is therefore the key to sustainable bio-foam, provides a remedy.
The ETH Zurich is still looking for future partners to realise the pilot project. The material is suitable for packaging material on the one hand and for the footwear industry on the other. The material innovation can be used to produce sustainable soles and flip-flops. It is to be hoped that the paradigm shift in textile production will prevail in the long term and that a drop will soon turn into a shower of rain on a hot stone. And in the case of plastic flip-flops, wearing them will no longer be a "walk of shame" in future.
When I’m not exploring the depths of the sea as an open water diver, I enjoy plunging into the world of fashion. On the streets of Paris, Milan and New York is where I keep my eyes peeled for the latest trends. And I’ll show you how to take them from the catwalk to your everyday life.