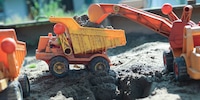
Background information
Fisher Price, we need to talk!
by Ann-Kathrin Schäfer
Making sustainable sportswear in Switzerland was Michael Ingram’s dream. Many thought it was impossible. With his start-up Revario, he’s showing sceptics that perseverance and flexibility pay off – not only when it comes to trail running, but also when making a business idea a reality.
It all started in a kitchen with a sliced-up shoe. Michael Ingram is a passionate trail runner who has competed in the Eiger Ultra Marathon, the Swiss Canyon Ultra Trail and many other races up to 120 kilometres long. He completed his first trail at the age of 12, long before trail running became established as a sport trend. What he loves even more than the physical and mental challenge is experiencing nature in the mountains.
But he has seen more and more changes in nature in recent years. However, just pointing out the problem isn’t for him. Michael wanted to help solve it himself. His shoes seemed a good place to start, because they were largely made of plastic, manufactured in Asia and only had a short lifespan. «There has to be a better way,» he said to himself and cut open his running shoes with a kitchen knife to get an insight into the structure and possible manufacturing methods.
In the short term, cutting up the shoe was in vain. Despite intensive efforts, Michael realised that making sports shoes in Switzerland with sustainable raw materials – as he intended – wasn’t possible at the time. But if there was one thing he learned from running ultra-distances, it was that giving up isn’t an option and that it takes perseverance to achieve a goal. So, he set his sights on the next milestone: producing trail running clothing from recycled materials in Switzerland.
He has achieved this goal. We meet in the tailoring studio of his brand Revario in Marly to the south of the city of Fribourg. This is where a new eco district is currently being built, in the former industrial district where Ciba, Sandoz and Ilford Imaging were once based. Residential buildings, an innovation centre, restaurants, an escape room and a swimming pool have already been completed. Other buildings are still under construction. The atmosphere has something of a departure about it, a new beginning. Revario has just moved into a larger studio and space is once again running out, says Michael, who runs the company with his business partner Emmanuel Currat.
The start-up atmosphere suits Revario, which was only founded at the beginning of 2020 and has grown significantly since then. After cutting up his running shoe, Michael focused on clothing and contacted recycled fabric suppliers, who initially didn’t take him seriously. Michael wanted to make garments in Switzerland with sustainable materials, and that – experts agreed – was a crazy idea. «Not economical,» said some. «There’s no longer any processing expertise for technical materials in Switzerland,» warned others. «In general, far too expensive and not at all feasible,» said yet more. All good reasons for Michael to give it a go anyway. Because having sportswear manufactured in Asia doesn’t fit with his ideas about sustainability due to the transport routes. He finds it even more absurd when the label says: «made from Italian fabric,» but then it’s made into a shirt in Asia.
After he made the first prototypes of a trail running vest at home with the help of a local seamstress, he saw the potential. At the same time, he heard about a Caritas vocational reintegration initiative that was looking for a project for seamstresses. He presented his project on a crowdfunding platform run by Geneva-based energy supplier SIG. The response exceeded his most optimistic expectations. 600 items of clothing from his new brand were ordered within a month. Now production could start.
Since then, growth has been steady. In its second year, Revario has already sold 3,500 items of clothing and is expected to sell around 10,000 by the end of 2023. The number of employees – almost all of them seamstresses – has increased to 10. And a wider selection of materials are now processed. Michael recently came across a fabric made from recycled car tyres through a supplier. He now uses this material to make hoodies and leggings that feel surprisingly soft and comfortable. His employees also sew textiles from recycled PET bottles. For many products, the Revario website states how far the fabric has travelled. It’s usually a few hundred kilometres.
While sewing machines whir in the background, Michael shows me another advantage of local production. When the clothing industry moved to Asia, only a few textile suppliers remained in Europe. They specialise in high quality and sustainability. That means that finding textiles like the ones he’s looking for isn’t as difficult as you’d expect.
Michael also has an eye on natural materials. However, the demand for synthetic technical materials is high in trail running because wool or other materials aren’t as light and fast-drying. He uses organically grown cotton from Greece to create a hoodie that’s also suitable for leisure time. Merino wool is relatively scarce in Europe, so it’s not yet an integral part of the collection. But the 38-year-old entrepreneur already has his sights set on fabrics made from wood fibres.
Local production with suppliers from the surrounding area has other advantages: Michael can react quickly when materials such as the fabric made from car tyres come onto the market. He also communicates with the trail running community via social media. «We constantly ask: do you want this or that? In what colours?» says Michael. Suggestions, criticism and ideas flow directly into the next designs.
Local production has opened up another significant line of business: team shirts for clubs and companies. Revario can make tops, shorts and hoodies with an individual logo for a minimum order as low as 10 garments. The sustainable materials, small order quantities and fast delivery times are a plus for many customers.
For Michael, there’s a key difference between his new job and trail running: as an entrepreneur, there is no finish line. As with trail running, the surroundings and conditions changed, but he never reached the end. In the future, he intends to continue to expand the collection and perhaps open new locations. «It would be great to have production in Germany for the German market and in Italy for the Italian market.» He wants to remain close to customers and suppliers. It’s also important to him to extend the lifespan of his clothing. That’s why he offers a repair service. Damaged garments can be returned and repaired in the studio.
He has another goal in mind: he rejected the idea of producing a sustainable running shoe in 2020 because there was no expertise in Switzerland to sew the upper material. He has now built up sewing expertise in Marly in the canton of Fribourg, so making a shoe is possible again.
Header image: Siri SchubertResearch diver, outdoor guide and SUP instructor – I love being in, on and around water. Lakes, rivers and the ocean are my playgrounds. For a change of perspective, I look at the world from above while trail running or flying drones.