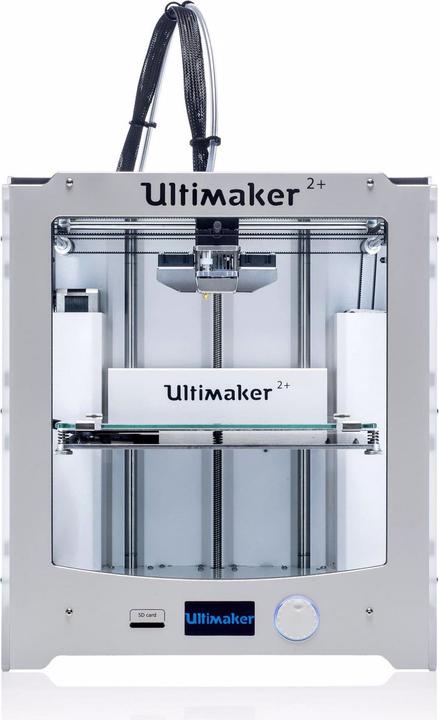
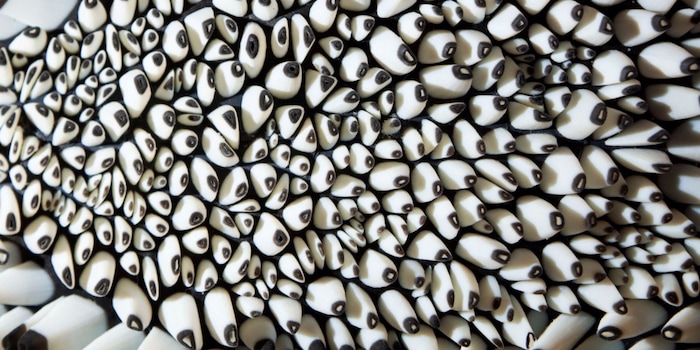
The fabric of the future

Wearable tech is not just about smartbands and watches, glasses and similar gadgets.
Will the stuff of dreams soon be the stuff of recording dreams?
Slowly but steadily and with increasing sophistication, technology is also finding its way into suits. Nowadays, garments are produced in part or even in their entirety using 3D printers. The second skin thinks for itself or even provides insights into the wearer's emotional world. The following is a brief overview.
Digital prints
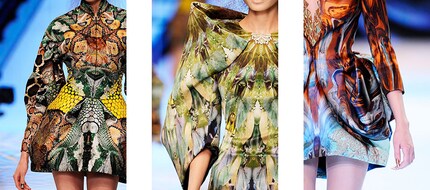
Digital prints had their big moment in the spotlight at the end of 2009 at the summer shows for the following year. Above all, the creations of the "enfant terrible" in the fashion Olympics, Alexander McQueen. In his "Platos Atlantis" collection for summer 2010, he presented digital prints at the highest level. Completely computer-generated graphics on heat-treated and laser-cut materials have never looked better. Whether silk, cotton, mousseline or even leather - the majority of the 45 looks came into contact with state-of-the-art technology. Architectural software was also used for many pairs of shoes. The shoemaker was not responsible for the production. They were calculated on the computer, moulded from synthetic resin and polished to a high gloss.
Colourful prints are taken to the extreme by designer Mary Katrantzou. The London-based Greek designer is a master of digital prints and has perfected both her aesthetic and the process used to create her ready-to-wear garments in recent years. Patterns and prints are created on the computer and precisely arranged using software.
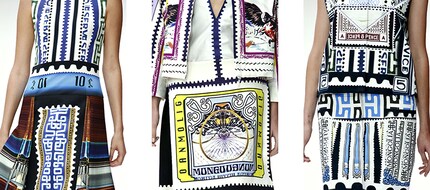
Digital printing refers to a group of printing processes in which the printed image is transferred directly from a computer to a printing press without the use of a static printing form.
3D printing
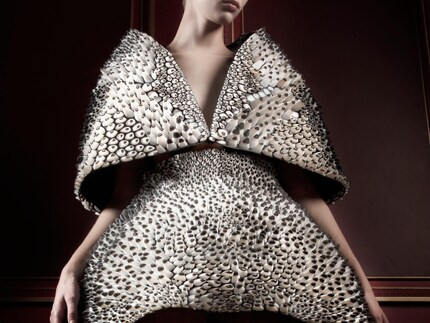
Many areas are suitable for 3D printing. In addition to the industries that spring to mind, such as architecture or prototyping, 3D printing can also be used in jewellery or fashion. The first fashion designer to adopt this principle in her process was the Dutch designer Iris van Herpen. Frustrated by the limitations of traditional materials, she began experimenting with 3D printing during her studies - in collaboration with architects and scientists. Since then, she has been exploring the limits of what is possible.
Her collections have a strong sculptural flavour, precisely because of the extensive use of 3D printers. Although peculiar in appearance, they are never unwearable. An absolute highlight of her work to date is the "Anthozoa" ensemble. Thanks to the 3D specialists at Stratasys and their "Objet Connex" printer, as well as the help of a specialist professor, it was possible for the first time to combine several hard and soft materials in one item of clothing.
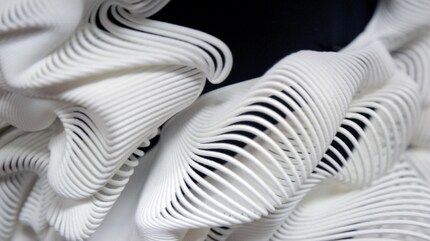
In 3D printing, three-dimensional workpieces are built up layer by layer. The build-up is computer-controlled from one or more liquid or solid materials according to predefined masses and shapes. Physical or chemical hardening or melting processes take place during the build-up. Typical materials for 3D printing are plastics, synthetic resins, ceramics and metals.
Conductive yarn
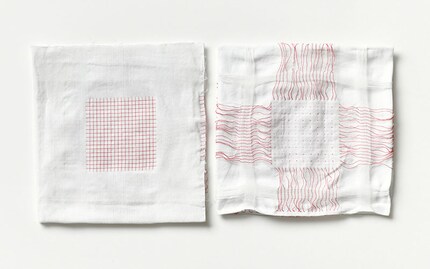
The "Project Jacquard" project initiated by Google and running under the ATAP banner makes it possible to spin conductive threads with commercially available yarn and weave them in the traditional way. This turns everyday objects such as clothing and furniture into interactive companions.
The conductive yarn is made from a thin metal alloy and traditional materials such as cotton and silk - there is no discernible difference to conventional yarn. It allows customised solutions such as touch sensitivity and gesture control. The collected data can be transmitted wirelessly to devices such as smartphones or laptops and analysed.
The associated technology has been developed to be as unobtrusive as possible and many of the components required are no bigger than a suit button.
Will a suit - spun from such yarn - recognise our emotions, know how we are feeling and record our dreams for evaluation afterwards? The future will tell.
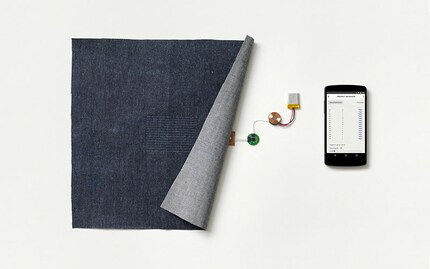
Products on the topic
You might also be interested in:

